Light materials are crucial when reducing the emission of greenhouse gasses in areas such as the transport sector and production of energy. In the new EU funded project HyFiSyn researchers from DTU Wind Energy, among others, are going to work for making light and strong materials for the industry during the next three years. The goal is to be reached by using so-called hybrid composites.
At DTU Wind Energy researchers are working with hybrid composites which are composite materials created from two types of fibres, e.g. glass fibres and carbon fibres. The vision is creating a material which is strong as well as light. Carbon fibres weigh less and are stronger than glass fibres but they are more expensive, too. However, a larger elongation of the glass fibres is possible, compared to the carbon fibres, which leads to synergy between the two fibres: The hybrid composite becomes stronger compared to what might be expected from a simple mixing of the two kinds of fibres. Combining the fibres in a hybrid composite means a possibility of creating a lighter and stronger material and reducing the cost of the material.
The structure of the material is important
A light and strong material is necessary if it is going to be part of e.g. wind turbine blades. Head of Section at DTU Wind Energy Bo Madsen is part of the project. He explains the importance of the order of the two kinds of fibres in the plastic material which surrounds the fibres in order to reach the synergy between the fibres, and to reach the highest achievable strength of the material. The order of the fibres is called the microstructure.
“Our focus is at the microstructure”, Bo Madsen explains. “We are working experimentally and look into the manufacturing technique, i.e. the combination of glass fibres and carbon fibres in the hybrid composite, and how to achieve a controlled microstructure”.
The figure shows a schematic drawing of the three ways of which the two fibres may be distributed in the hybrid composite: layer-layer mixing, bundle-bundle mixing and fibre-fibre mixing. The microstructure is investigated by using optical and electron microscopy as well as advanced techniques such as 3D x-rays.
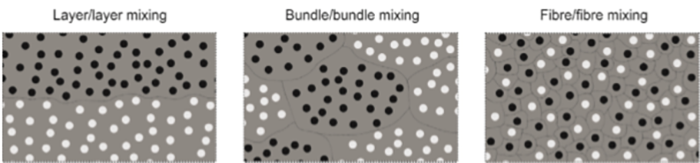
International and national cooperation
DTU Wind Energy has hired a PhD student for the job. Next February he will come the long way from India to DTU when the project is to be jump-started. HyFiSyn is a Marie Curie project from Horizon 2020 Research and Innovation programme. The purpose of the programme is supporting the education and mobility of young researchers and subsidies are given to international students. The PhD student is one of 13 young researchers from eight universities who participate along with five partners from the industry. The researchers all work with development of hybrid composites for the transport and energy sector.
The Danish company Fiberline is part of the project to find out what is possible to realize industrially. Fiberline is going to manufacture the hybrid composite and will translate research into practice.
In the long term, the composites might be used in the wind turbine blades of the future. Bo Madsen explains: “With the development of the hybridcomposites an important step is reached regarding the work for realizing the requirements of the future materials for long and strong wind turbine blades”.