At the project BIO4SELF researchers study bio-based materials, with the vision to develop sustainable materials for many purposes in the industry. The researchers from DTU Wind Energy now have got the formulation for the material in order to use it in load bearing contexts – and in the long term in wind turbine blades.
Within the BIO4SELF project, DTU Wind Energy’s researchers are using bio-based plastic which is made of biodegradable and sustainable resources; organic material for instance corn. To produce the plastic, microorganisms are fed with the corn. The outcome is lactic acid which is used for producing the material polylactate, called PLA. The PLA is a plastic material which can be spun into rigid, strong fibres where the individual fiber is thinner than a hair. PLA plastic is already utilised in the real world outside of the laboratories: the material is used at hospitals where PLA is utilised for dissolvable threads for operating wounds.
In the BIO4SELF project, Senior Researcher from DTU Wind Energy Bo Madsen calls the material “self-reinforced plastics”. It is built from PLA fibres, and a PLA matrix that binds the fibres together. The material is manufactured in a process involving high temperature, where the matrix is melted to surround the fibres. As both matrix and fibres are made from PLA, the challenge is to find the right process temperature in order to melt the matrix and not the fibres.
Sustainable properties
Project manager at DTU Wind Energy, Development Engineer Justine Beauson clarifies that the conditions under which the self-reinforced plastic material is to be manufactured have now been defined. Among the next challenges to overcome, the researchers will study what happens when the material is exposed to moisture from the surroundings. Because the PLA is made from organic material, it is sensitive to water. Thus, the performance of the plastic is reduced in a humid environment. In order to reduce the moisture sensitivity of the material, to make it more durable, so-called additives are added. Another challenge for the material is what time does to it, that is ageing – a field which the researchers are going to look into, Justine Beauson tells.
The latest news from the BIO4SELF project is the development of the material in order for it to become capable of bearing large external loads. Bo Madsen explains:
“Now we have got the recipe of how to manufacture the self-reinforced plastic material, and we can start to think about how it can be utilised in load-bearing constructions. Initially we expect the material to be part of components in washing machines and cars.”
Has to be recyclable
The ambition of the project is to manufacture reinforced plastics which are easy to reuse in other connections. Thus, research has aimed at producing composite materials where the fibres and the matrix are of the same material. Such material is much easier to recycle compared to conventional composite materials, such as glass fibre composites, consisting of two different kinds of materials.
When the self-reinforced plastic component is no longer useful there is yet another environmental benefit to gain: Because the PLA is bio-based it can be decomposed biologically at the right temperature and humidity. In this way, turning the plastic into trash can be avoided.
The industrial partners in the BIO4SELF project are looking forward utilising the final sustainable PLA material. One of them is the Turkish company Arcelik which produces all kinds of consumer goods. Orkun Kaymakçı, R&D Specialist, says about the material of the BIO4SELF project:
“With the company vision ‘Respects the Globe, Respected Globally’, Arcelik is committed to use sustainable and eco-friendly materials in its products without sacrificing the quality. The fully bio-based, high mechanical property, self-reinforced PLA composite that will be developed during the BIO4SELF project will be the perfect alternative to its fossil based counter-parts for Arcelik products.”
At the moment the researchers are also working on the manufacturing of prototypes of products, which might become part of household machines which we all use every day.
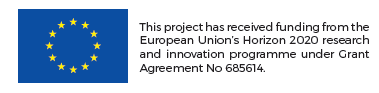