The blades on today’s giant wind turbines are simply enormous. And they have to be able to withstand extreme impacts. This is quite a challenge, but the wind industry has now teamed up with researchers to develop a bio-based composite material that is also highly robust.
By Signe Gry Braad
Even though most wind turbines seem to resemble each other very closely, an industry expert would be quick to point out that in no way is a wind turbine ‘just a wind turbine’.
One of the fundamental differences between them is the production of the huge turbine blades that have to be able to withstand a bit of everything. Briefly put, the blades consist of layers of fibre-reinforced plastic, also called ‘composite materials’. These materials are made of dry glass fibres or carbon fibre, which is soaked with sticky resin that glues the fibres together and then solidifies.
Two different types of resin have conventionally been used in the process to soak the composite material: polyester and epoxy.
|
|
The giant wind turbines of today are the result of many years of development and optimization of aspects including the composite material used to make the blades.
|
Polyester and epoxy
Polyester is a material that flows readily and hardens quickly, but it also has two major drawbacks. Firstly, the long-term durability of the material is a problem, which entails significant expenses for maintenance. Secondly, polyester must be mixed with the hazardous substance styrene in order to harden. This involves implementing an extensive series of precautions when working with the material.
An alternative is to use epoxy. Epoxy hardens through a more complex chemical process, where the mix ratios must be very accurate if the material is to harden properly. In addition, it is a more viscous material, which makes it difficult to ensure that all the glass fibres are thoroughly soaked. On the other hand, epoxy is not decidedly hazardous to health, and the finished fibre laminate is much stronger than comparable styrene composites.
It is therefore clear that neither of the two materials ticks all the boxes and for this very reason, many people in the wind industry have long been dreaming of a better solution.
No tradition for partnership
This is the dream that is laying the foundations for a unique partnership between Siemens Wind Power, the Swiss-Dutch composite company DSM, the Belgian fibreglass manufacturer 3B and researchers from DTU Wind Energy. All the partners are experienced operators in the field of wind energy.
Partnerships of this kind are otherwise uncommon in the wind industry, where players prefer to keep their cards close to their chest.
"The new composite system represents the best of both worlds: optimal process properties, no styrene emissions, and excellent composite interaction."
Povl Brøndsted, DTU Wind Energy
“Previously, for example, fibreglass manufacturers would flatly refuse to tell us what they used in their mixes—as did the polymer producers. They were most unwilling to share their knowledge. However, the fact of the matter is that we need more openness in the industry if we’re to develop new ideas, and a number of the manufacturers in this field have—thankfully—finally woken up to this idea,” relates Professor Povl Brøndsted, who is a research specialist at DTU Wind Energy and has functioned as both material expert and consultant on the project.
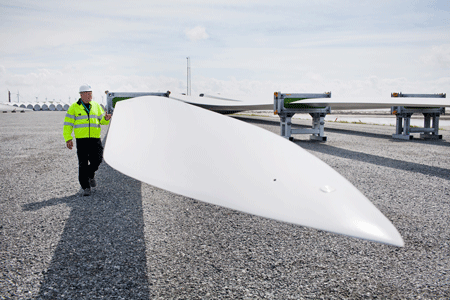
New solution
Working together, the partners have now developed a new system based on a composite material created by DSM. The new material is 40 per cent bio-based, and it does not contain the hazardous substance styrene. In addition, 3B has found a way to optimize and reinforce the fibreglass material used in the composite system.
“The new composite system represents the best of both worlds: optimal process properties, no styrene emissions, and excellent composite interaction—which translates into mechanical properties on a par with the epoxy-based composites,” explains Povl Brøndsted.
What is more, the net working time with the material has been reduced because the actual packing and hardening phases are shorter. This is a very important factor in an industry where one of the competition parameters is how many hours it takes to make the individual blades.
Award-winning product
The parties involved in the project are not alone in identifying the potential of the new composite system. In spring 2014, the project was honoured with a JEC Innovation Award—one of the most prestigious prizes awarded in the field of composite technology. It is a mark of recognition that means a great deal to the team behind the new product.
“Viewed from the perspective of research, an award like this serves to emphasize that we are still leading the way in the area of wind energy in Denmark. Personally, I am sure that it will generate more attention in the business community than 100 publications could possibly do,” says Povl Brøndsted from DTU Wind Energy.
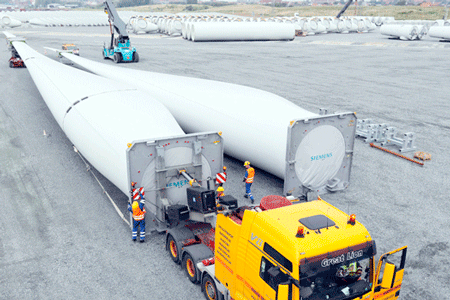
Modern turbine blades are up to 55 metres long and can weigh more than 10 tonnes. As a result, the new material must be tested from every conceivable perspective to ensure it behaves precisely as expected.
|
Promising future
However, there is still a lot of work to be done before the first turbine blades made using the new composite material roll off the production line. Povl Brøndsted and his team are currently searching for ‘the snake in paradise’, as they themselves put it. In layman’s terms, this means that they are testing the material from every possible angle.
“Up to now, we have been working with weights of just a few kilos—so there’s a very long way to go up to a 55-metre blade weighing in at over 10 tonnes. And we have to be absolutely sure how the material behaves before we dare release it for full-scale production,” says Povl Brøndsted.
As soon as all the various elements have been duly ticked off, Siemens is ready to switch its systems from epoxy to the new product, which has been named Beyone.
Article from DYNAMO no. 38, DTU's quarterly magazine.